高效能智能升级 松下PLC编程软件赋能工业自动化新纪元
19429202025-03-25下载排行17 浏览
工业自动化走到今天,传统PLC编程的局限性还能被忽视吗?
在工业4.0浪潮下,生产线对控制系统的实时性、灵活性和智能化要求越来越高。许多企业仍在使用传统PLC编程软件,面临开发效率低、跨平台兼容性差、维护成本高等痛点。例如,某汽车零部件厂商曾因旧版软件无法支持多任务处理,导致生产线升级延迟3个月,直接损失超千万元。这不禁让人思考:高效能智能升级 松下PLC编程软件赋能工业自动化新纪元的路径究竟在哪里?
1. 传统PLC编程能否应对复杂场景?
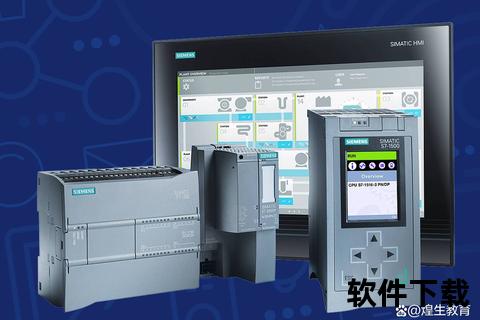
传统PLC编程常被诟病为“代码冗长、调试困难”,而松下PLC编程软件通过模块化设计大幅提升了开发效率。以FPWIN Pro为例,其符合IEC 61131-3标准,支持梯形图(LD)、结构化文本(ST)、顺序功能图(SFC)等多种语言,用户可根据需求灵活切换。例如,某食品包装企业利用FPWIN Pro的ST语言编写灌装控制逻辑,将原本需2000行梯形图代码简化为500行结构化文本,开发周期缩短40%。
更值得一提的是,Control FPWIN GR7的“多型号兼容”特性解决了老旧设备升级难题。该软件支持FP0R、FP7等十余种PLC型号,甚至能通过自定义通信协议恢复停产设备功能。某化工厂通过GR7成功激活一台库房闲置的FP0R型PLC,仅花费70元自制编程电缆,便替代了价值数十万元的新设备投入。这种“软硬协同”的升级模式,正是高效能智能升级 松下PLC编程软件赋能工业自动化新纪元的典型案例。
2. 跨品牌协作能否打破数据孤岛?
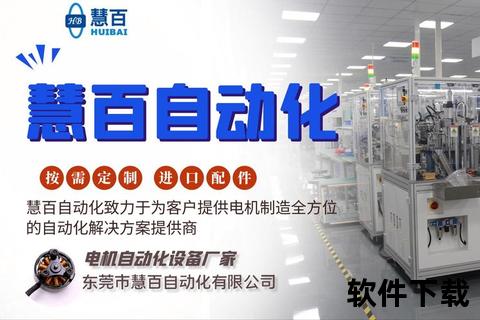
工业现场常存在多品牌设备并存的局面,数据互通成为痛点。松下通过开放生态策略,推动软件兼容性突破。例如,GX Works2虽为三菱电机开发,却能适配松下FP系列PLC,支持跨品牌设备组态。某电子厂利用该软件统一管理三菱伺服电机与松下FP-XH PLC,实现运动控制指令毫秒级同步,良品率提升12%。
CODESYS平台的开放式架构成为跨品牌协作的另一利器。某新能源电池生产线采用CODESYS对松下PLC与西门子HMI进行集成,通过OPC UA协议实现实时数据交互,将设备故障诊断响应时间从30分钟压缩至5分钟。这种“以软件定义硬件”的模式,不仅降低企业改造成本,更让高效能智能升级 松下PLC编程软件赋能工业自动化新纪元从愿景走向落地。
3. 智能化升级如何释放边缘计算潜力?
随着工业大数据爆发,传统PLC的算力瓶颈日益凸显。松下FPWIN Pro的创新性在于引入边缘计算能力,其支持的多核CPU架构可将视觉检测、能耗优化等任务分流处理。某机床制造商利用该功能,在FP7型PLC上同时运行刀具磨损监测算法与主轴控制程序,将设备停机率降低25%。
更前沿的探索体现在TIA Portal的深度应用。尽管是西门子开发的软件,其与松下PLC的兼容性已通过Profinet协议实现。某钢铁厂通过TIA Portal将松下PLC与AI预测性维护系统对接,提前48小时预警轧辊轴承故障,避免单次事故损失超百万元。这些案例证明,高效能智能升级 松下PLC编程软件赋能工业自动化新纪元的核心在于让控制层兼具感知、计算与决策能力。
从工具升级到生态重构:企业如何抓住机遇?
对于工业企业,建议分三步走:
1. 诊断现状:梳理现有设备型号,优先通过GR7等兼容软件激活老旧PLC价值,如某纺织厂通过版本迁移让20台FP1型PLC重获新生;
2. 选择平台:中小型企业可依托CODESYS降低开发门槛,大型项目则推荐FPWIN Pro与TIA Portal组合方案;
3. 培养人才:建立梯形图与结构化文本的双语开发能力,参考某汽车厂“1名工程师+3个月培训”的人才孵化模式。
正如上海工业自动化仪表研究院彭瑜教授所言:“PLC的进化不是替代,而是融合。”当控制软件既能向下兼容硬件遗产,又能向上对接智能生态,高效能智能升级 松下PLC编程软件赋能工业自动化新纪元才真正展现出颠覆性力量。
--